

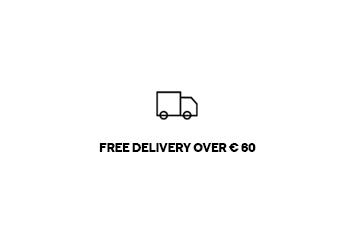
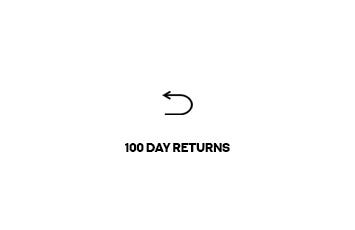
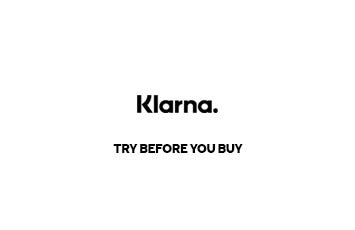
JACK & JONES NO
Welcome to JACK & JONES, your ultimate destination for men's clothing and shoes! Whether you're into keeping up with the latest trends or a die-hard denim enthusiast, we've got you covered.
Since 1990, our mission has been to provide you guys with the coolest clothes for every occasion. At JACK & JONES, we're all about staying ahead of the curve when it comes to men's fashion trends. From streetwear staples to classic essentials, we've got the styles that will keep you looking fresh and on point.
At JACK & JONES, we believe that nobody should go without a stylish wardrobe. Whether you're big, small, young, or old, there's something for everyone. That's right, we offer trendy plus-size clothing for men and cool clothes for young boys too.
We're all about jeanswear and designing cool denim clothes, but we're not stopping there. From killer denim styles to dope bomber jackets and classy suits, we've got everything you need to upgrade your wardrobe and turn heads wherever you go. We've got you covered from head to toe, whether you're dressing to impress on a date, chilling with your friends, or a smart-casual outfit for work. Need to upgrade your wardrobe with trendy accessories? Don't forget to
check out our men's underwear & shoes and upgrade your style today!
Men's Fashion Trends
Besides our classic collection of men's clothing essentials, we're always on the lookout for the newest styles and must-have pieces. Stay stylishly updated with the latest arrivals from JACK & JONES and browse our newest styles today. From cool denim jackets to classic chino trousers, make sure not to miss out on those and more upcoming must-haves.
Passion for Denim
If there's one thing, we're passionate about at JACK & JONES, it's jeans. We believe that denim is the ultimate statement piece. That's why we've curated an extensive collection of denim pieces that are perfect for every style and occasion. From the latest trends to our handy jeans fit guide, find out everything about this cool blue fabric and how to rock it. As denim experts, we’ve got some special collections just for you. Discover the coolest pair made of Indigo Knit, the best quality material provided directly by the best Italian designers, super stretchy styles and our low-impact denim collection. If you are as crazy about denim as we are, check out our latest denim collection and join the denim brotherhood today!
How Men's Jeans Should Fit
Jeans are spot on when they fit exactly right and feel perfect for your personal style, not too tight or too loose, and you can't wait to wear them all day. Get to know our fits and styles through our different denim buddies: Liam, Tim, Mike, and Fred. Whether you are looking for the coolest pair of skinny jeans or the perfect fit in tapered jeans, JACK & JONES has the styles to match your preferences and elevate your denim style. Are you still unsure what size or fit to choose? Don't sweat, with our jeans fit guide you can find the perfect pair that suits you perfectly. We've made it easy for you to find your perfect pair, so once you've nailed your fit, just keep an eye out for your denim buddies and skip the hassle of trying to find the right fit.